Waterproof basement
We have been waterproofing basements with the electrophysical DRYMAT® system since 2010. In this guide, we provide an overview of the advantages and disadvantages of the various methods.
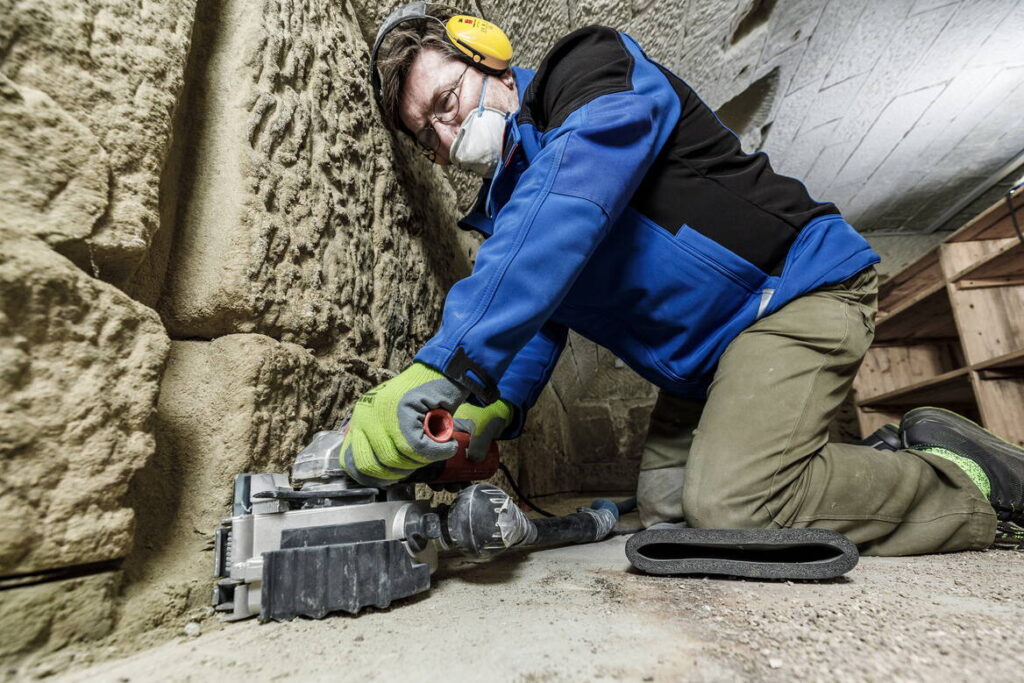
How to waterproof the basement?
- How do damp basement walls?
- What requirements should meet a basement waterproofing?
- What are the sealing methods?
- What are the risks associated with manual waterproofing methods?
- What are the advantages and disadvantages of electrophysical sealing?
- Why is electrophysical sealing controversial in practice?
- What are the arguments against building dryers?
- How much does basement waterproofing cost?
- Conclusion
Core statements
- For effective waterproofing, the causes of moisture must first be identified. The most common causes are defective installations, damage to the building envelope, pressing moisture sources or capillary rising damp in the walls. Often, several causes overlap.
- Optimal basement waterproofing mitigates or eliminates the cause of moisture, keeps the entire building structure permanently dry.
- With the horizontal barrier, the area below the barrier remains damp; the interior vertical barrier cannot protect the wall from moisture penetration on the outside and below. With the external vertical barrier, the wall below is also not protected from moisture.
- Electrophysical wall dehumidification works actively against moisture and dries the entire building structure down to the basement floor. However, the method alone is not effective in the case of pressing moisture and damage to the building envelope.
1. How do damp basement walls?
The most common causes of damp basement walls are
- Condensation
- Defective installations and damage to the building envelope
- Rising damp in the basement wall
- Pressing water
In most cases, several causes of moisture overlap. Therefore, it is worthwhile to have the building inspected by experienced building experts. In the following sections, we will go into detail about the damage mechanisms of the individual causes.
When moist air meets a cool surface, condensation occurs, for example on the outside of a cool glass bottle. In the case of buildings, this leads to consequential damage over time, such as mold growth, musty odors and decomposition of the building fabric. The reasons for high humidity are often incorrect ventilation, water vapor from showers, cooking or drying laundry. Because warm air can absorb more moisture than cold air, ventilation should be carried out at the coolest time of day if possible.
Inadequate installations on the house often lead to moisture damage. Examples of such installations are flat roofs, gutters, downpipes, cisterns, rain barrels; the condition of bricks, stones, mortar, plaster, wall bases, weatherproof paints, damp-proof courses and silicone joints; weak points in the building envelope, such as cracks in brickwork and flashings; structures that conduct water to the masonry, including leaky windows and doors, heat exchangers or ventilation vents; chimneys and rain deflectors.
The phenomenon of capillary rising damp in the building fabric occurs because the wall is naturally negatively charged. Thus, the building substance absorbs moisture into itself, much like a sponge. In the three causes of moisture discussed, the real problem is not the leakage of the basement wall, but either the habits of the people in the house, defects in the installations on the house or the physical properties of the building substance.
In other words, basement waterproofing is usually not about «waterproofing» in the first place, but about identifying and eliminating the causes that lead to moisture in the building structure. Therefore, you should not think about appropriate methods of basement waterproofing until you have clearly identified the causes of moisture. To do this, it is worthwhile to consult building experts on moisture.
In rare cases, an oppressive moisture source may be the cause of basement wall moisture penetration. Oppressive moisture includes slope, strata or periodically high groundwater, as well as springs or other water veins near the building. Pressing moisture usually means that the building was constructed in an unfavorable location. However, heavy moisture penetration is not yet an indication of pressing water.
2. What requirements should meet a basement waterproofing?
An optimal basement waterproofing
- Eliminates or mitigates the causes of moisture
- Keeps the building fabric completely and permanently dry
- Interferes as little as possible with the building fabric
Deep interventions in the building fabric involve static risks and the danger of consequential damage, such as cracks or stress redistribution. They should therefore only be carried out, especially in old buildings, if there is no gentler alternative (cf. Methods of waterproofing under 3.).
Hermetic sealing of the basement is fundamentally undesirable, as the wall can then no longer «breathe». This usually leads to consequential damage that does not necessarily have to be visible. For these reasons, impermeable barrier layers should only be implemented if all other methods fail to achieve the desired result. This applies in particular to the case of an oppressive source of moisture (cf. Causes under 1.).
3. What are the sealing methods?
To seal leaking basement walls, there are basically three options:
- Vertical barrier: A large-area waterproof barrier layer is applied to the outside or inside of the wall, such as a bitumen coating or slurry plaster.
- Horizontal barrier: at a certain height of the wall is installed waterproof barrier layer, which crosses the entire diameter of the wall.
- Electrophysical barrier: By installing electrodes, a positive electrical potential is induced in the wall, which protects the wall from moisture penetration.
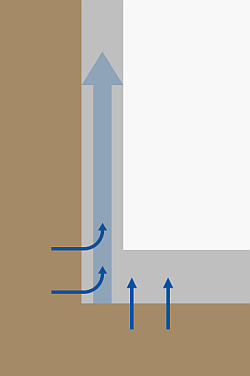
Rising damp
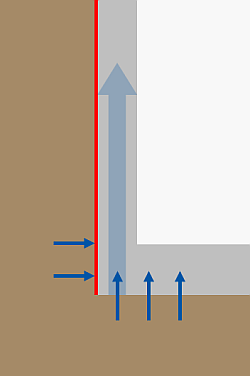
Principle of the vertical barrier
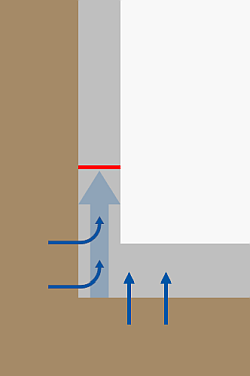
Principle of the horizontal barrier
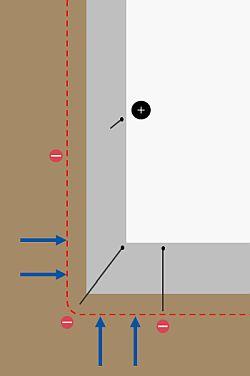
Electrophysical barrier
While horizontal and vertical barriers are easy to understand in principle, electrophysical waterproofing requires a more detailed explanation: When moisture rises, water can rise up the capillaries (narrow «tubes», crevices or cavities) of the building material. This effect is also called the «capillary effect», or «suction tension», and occurs naturally because the building material has a negative electrical charge.
As part of the electrophysical sealing process, a positive electrical potential is induced in the wall. «Electroosmosis» occurs: the capillary effect is neutralized. As a result, no new moisture can rise or penetrate the building fabric. The residual moisture evaporates over time, the wall becomes permanently dry down to the cellar floor. Electroosmosis also copes with a strong moisture load - in the case of pressing water or if the building envelope is damaged by cracks, it is only able to dry the penetrating moisture faster.
4. What are the risks associated with manual sealing methods?
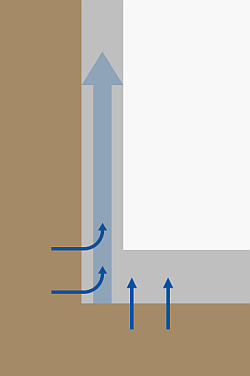
Rising damp
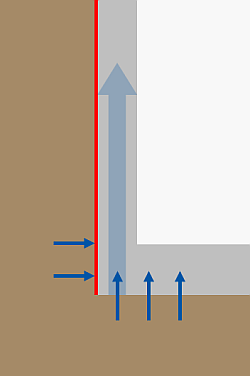
Principle of the vertical barrier
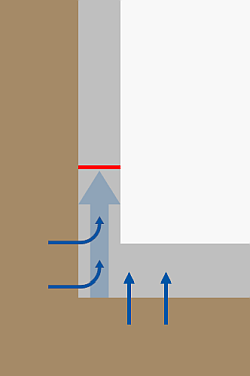
Principle of the horizontal barrier
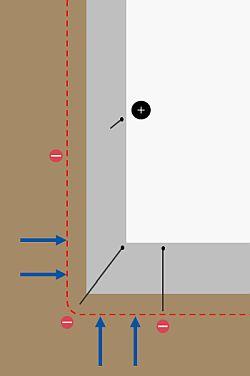
Electrophysical barrier
Optimum basement waterproofing firstly mitigates or eliminates the moisture problem, secondly keeps the entire building structure permanently dry and thirdly can be implemented with minimal invasiveness. How well do vertical and horizontal barriers meet these three requirements?
Horizontal and vertical barriers only solve the moisture problem inadequately: with a horizontal barrier, the area below the barrier, such as the cellar floor, remains damp; the interior vertical barrier cannot protect the wall from penetrating moisture on the outside and below. With the external vertical barrier, the wall below is also not protected from moisture.
Exterior vertical barriers are also very complex and expensive to install, especially as the basement wall has to be completely exposed. Horizontal barriers are less complex in comparison, but require deep structural interventions in the masonry, which can be structurally tricky. It is better to refrain from doing this, especially in old buildings.
5. What are the advantages and disadvantages of electrophysical sealing?
Electrophysical cellar dehumidification with the DRYMAT® system works actively against moisture and can permanently dry both cellar walls and cellar floors, even with high moisture levels. Thanks to the electrical potential, the dehumidified building fabric does not absorb any new moisture, but remains permanently protected from moisture (cf. Functionality in detail under 3.).
Thanks to its active effect, electrophysical sealing requires only minimal structural intervention and thus leads to considerable cost savings compared to vertical and horizontal sealing methods. The electricity costs for maintaining the electrical potential amount to approx. 50 EUR per year. This consumption is due to the control unit. No electricity flows in the wall and there is no exposure to electrosmog.
Electrophysical drying with DRYMAT® is also risk-free for people and the environment, has no impact on the building statics and is suitable for listed buildings. The DRYMAT® system works according to scientifically recognized principles and is certified according to Ö-Norm B 3355-2. Last but not least, you receive a 10-year guarantee on the control unit and a further 10 years from the ISO-certified manufacturer. More about our offer for basement waterproofing
6. Why is electrophysical sealing controversial in practice?
There are several suppliers and systems for electrophysical seals on the market. Some of them offer control units that build up a positive electrical potential exclusively via radio waves. In our experience, purely radio systems can only dehumidify your walls and floors but cannot dry out an entire building.
We have been the representative of DRYMAT® since 2010. The manufacturer is ISO 9001 certified for both the control unit and the application. The DRYMAT® system builds up the electrical potential via titanium electrodes installed in the wall. We have been using this system successfully for over 10 years and are therefore in a position to make a promise of success.
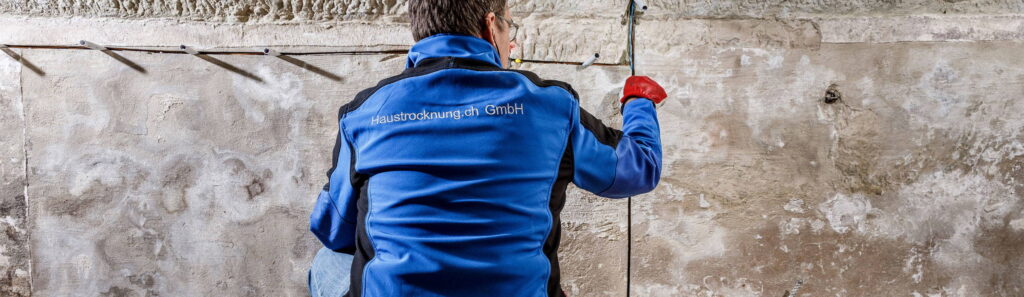
Installation of electrophysical basement waterproofing with the DRYMAT® system
7. What is the argument against building dryers?
Powerful building dryers are primarily suitable for drying buildings after water damage or during the construction phase. In the case of a moisture problem, however, where the wall absorbs moisture via the capillary suction tension of the building material, they can have a counterproductive effect: In this case, the building dryers actually lead to an increase in hygroscopy (wall can absorb more moisture from the air), while the cause of the dampness remains.
As a result, even more moisture gets into the wall in the medium term. The moisture also brings mineral salts into the masonry. These dissolved salts can crystallize. This results in an increase in volume, which in the long term leads to damage to the building fabric. The masonry then absorbs even more moisture due to salinization.
8. how much does basement waterproofing cost?
Electrophysical basement waterproofing with the DRYMAT® system costs around EUR 15,000 to 20,000 for a detached house with a floor area of 60 m2. This amount includes all work steps including analysis, installation and follow-up measurement 18 months after installation. Operating costs of around EUR 50 per year are added to this. Maintenance is not required.
In comparison, the cost of draining the same building with a drainage system is around EUR 45,000 to 60,000. The costs for the earthworks are particularly significant. Waterproofing alone costs around EUR 350 per square meter.
9. Conclusion
For successful basement waterproofing, the causes of the moisture must first be carefully determined. A specialist should be consulted here, as there are often several causes of dampness that can overlap. The most common causes are condensation, faulty installations on the structure, damage to the building envelope and rising damp within the wall.
If the problem is rising damp in the masonry without pressing water and without damage to the building envelope, electrophysical basement waterproofing is the most effective and cost-effective solution, as it actively combats damp and can be installed with minimal invasiveness. In contrast to electroosmosis, parts of the building structure remain damp with horizontal and vertical barriers.
We are the representative of DRYMAT®. This system comes with a guarantee of success, as both the system and the application procedure are Ö-Norm B 3355-2 certified.
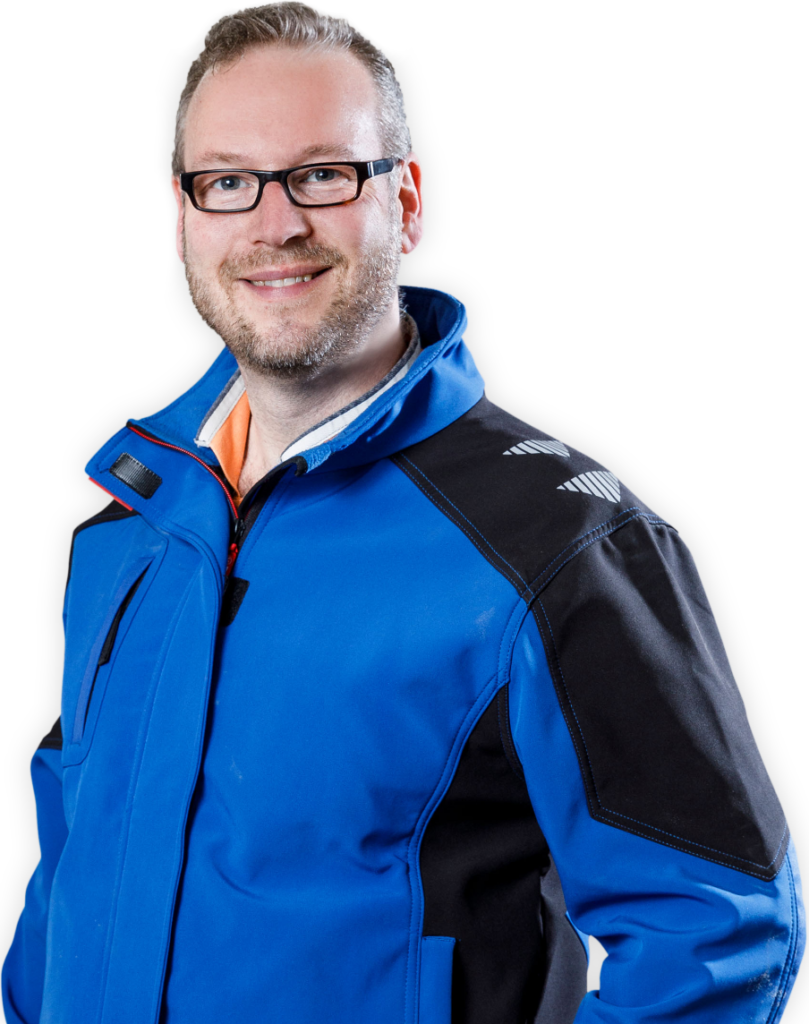
Contact us without obligation
Do you have any further questions or may we prepare an offer for you?
Get in touch with us without obligation. We look forward to your inquiry!
Get in touch with us without obligation. We look forward to your inquiry!
Tobias Bayer
Managing Director
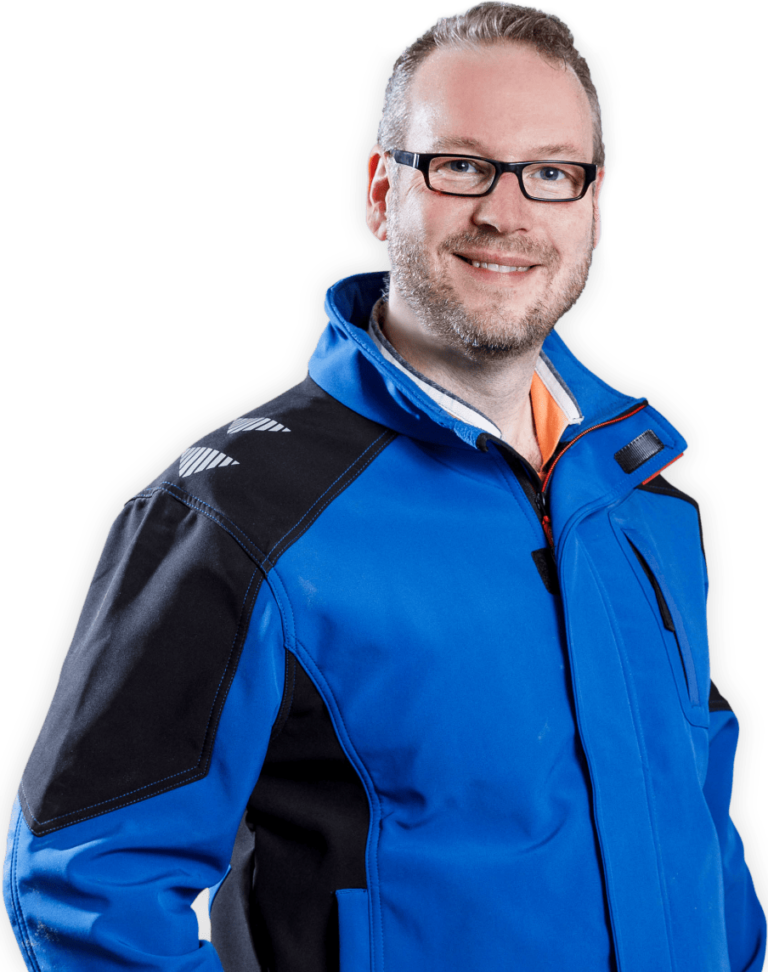